Achieve Optimal Performance With Durable Workshop Flooring Perth
Durable Workshop Flooring
Upgrade your workshop with PM Industries. Our expert team in Perth specialises in workshop flooring, offering a range of options to meet your unique needs.
Whether you require durable epoxy coatings for heavy machinery, slip-resistant surfaces for safety, or a visually appealing finish, we’ve got you covered.
Our flooring solutions are designed to withstand the toughest conditions, ensuring longevity and performance. We provide expert installation services, competitive pricing, and a commitment to excellence.
Elevate your workspace with high-quality flooring in Perth. Contact us today for a consultation, and let us transform your workshop into a functional, safe, and attractive environment.
How do I know if I need a new flooring?
You may need a new flooring if you experience any of the following:
Free Quotes Within 48 Hours
- Wear and Tear: If your current workshop floor shows signs of significant wear, cracks, or damage from heavy equipment and machinery, it’s time for an upgrade.
- Safety Concerns: It can improve safety by providing slip-resistant surfaces, reducing the risk of accidents.
- Aesthetic Upgrade: If you want to enhance the appearance of your workshop for a more professional look or to impress clients, the flooring can do just that.
- Improved Durability: It can handle heavy loads, chemicals, and constant foot traffic better than standard concrete floors.
- Compliance: Some industries require specific flooring types to comply with regulations, such as chemical resistance or electrostatic discharge protection.
- Easier Maintenance: It can make cleaning and maintenance more manageable, saving you time and effort.
Consult with a professional to assess your specific needs and determine if epoxy flooring is right for you.
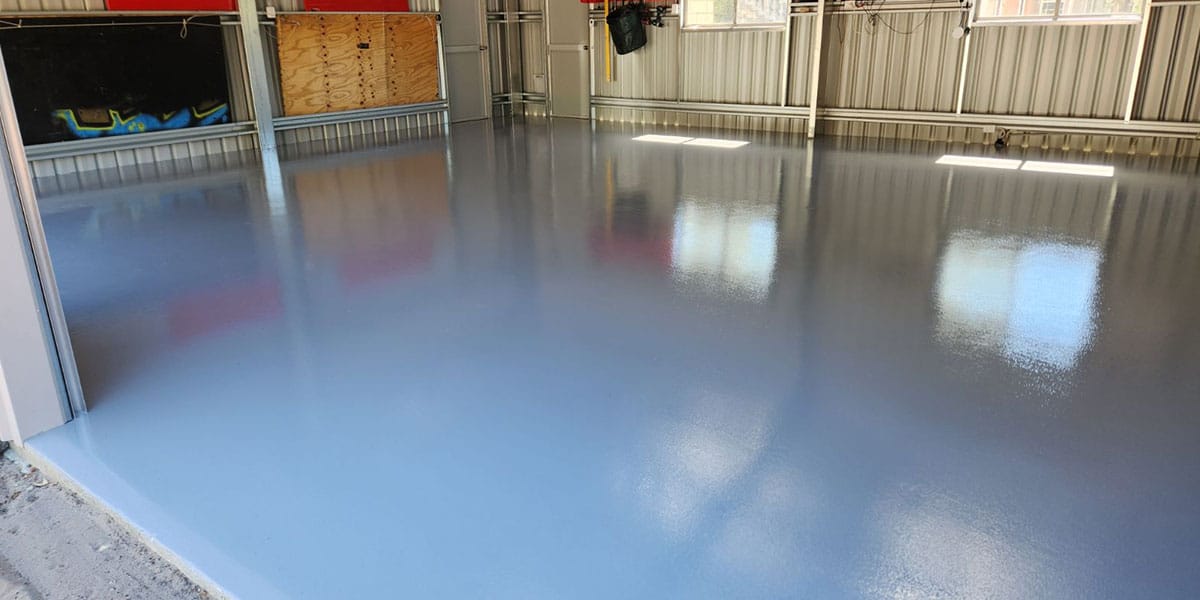
What factors affect workshop flooring costs?
The cost can vary significantly depending on several factors, including the type of flooring material, the size of your workshop, installation requirements, and any additional features or customisation.
There are several key elements to consider:
- Floor Size and Layout: Larger spaces will require more materials and labour. The layout of the workshop, including any unique shapes or corners, can impact the installation’s complexity and cost.
- Condition of Existing Floor: Floors that need significant preparation, such as crack repairs, levelling, diamond grinding or removal of old flooring, will increase the overall cost.
- Type of Flooring Material: Each material has different price points, with epoxy and polished concrete being popular for their durability and resistance to chemicals and stains.
- Customisation and Design Features: Custom features like coloured epoxy coatings, decorative chips, or specific patterns can enhance the aesthetic appeal of the workshop but will add to the cost. The complexity of the design and the number of colours used will influence the final price.
- Quality of Materials: Higher quality materials might be more expensive, but they typically offer greater durability and longevity, which is essential in a high-traffic environment like a workshop.
- Labour Costs: Skilled professionals might charge more but generally ensure a high-quality finish and better long-term performance.
- Installation Time: Some flooring types may have quicker installation processes but might not offer the same durability as those that take longer to install and cure.
- Geographical Factors: The location of the workshop can influence costs due to factors like accessibility, transportation of materials, and local labour rates.
- Project Complexity: The presence of obstacles, machinery, or the need to work around business hours can add complexity to the project and increase costs.
- Aftercare and Maintenance: Some flooring options may require specific maintenance routines or additional treatments over time. While these might increase the initial cost, they can contribute to the floor’s longevity and appearance.
It’s essential to get quotes from reputable flooring contractors in your area to get a more accurate idea of the cost of your flooring project. Consider factors like preparation work, labour, and any extra features you may need, as these can impact the overall cost.
How long does workshop flooring take to install?
The time it takes to complete a flooring project can vary widely based on several factors, including the type of flooring material, the size of the workshop, the condition of the existing floor, and the complexity of the installation.
Here’s a rough estimate of the timeframes for different flooring options:
- Epoxy Flooring: Epoxy coatings can typically be applied in several days to a week, depending on the size of the workshop and the number of coats required. Cure times may add a few extra days.
- Concrete Polishing: Polishing concrete floors may take a bit longer, ranging from one to two weeks, considering the grinding, polishing, and curing processes.
- Rubber Flooring: The installation of rubber flooring can usually be completed in a day or two, but this can vary depending on the complexity of the layout.
- Tiles or Interlocking Mats: Installing interlocking tiles or mats is generally a quicker process, often taking just a day or less, depending on the workshop’s size.
- Specialty Flooring: If you require specialized features or treatments, such as chemical-resistant coatings, the installation may take longer, depending on the complexity of the application.
It’s essential to consult with your chosen flooring contractor in Perth to get a more accurate estimate of the timeline for your specific project.
Factors like surface preparation, drying or curing times, and any additional customization can impact the overall duration.
Planning ahead and discussing the timeline with your contractor will help ensure that the installation aligns with your schedule and requirements.
How can I identify professional workshop flooring installer?
Identifying a professional installer is crucial to ensure a successful project. Here are some key factors to help you recognize a reputable and experienced flooring specialist:
- Portfolio: Ask for a portfolio or examples of their previous work. Professional flooring providers should have a portfolio showcasing different projects, which can give you a sense of their capabilities.
- Licensing and Certification: Verify that the company holds the necessary licenses and certifications for the type of flooring work they offer. This ensures they meet industry standards.
- Insurance: Make sure the company is fully insured. This protects you and the workers in case of accidents or damages during the installation.
- Transparent Pricing: They should provide clear, detailed quotes with no hidden costs. Be cautious of companies that are vague about pricing.
- Communication: Professionalism extends to communication. They should be responsive, answer your questions, and keep you informed throughout the project.
- Warranty: Ask about the warranty they offer for their work and materials. A reliable provider should stand by their products and services.
- Safety Practices: Ensure that they prioritize safety during installation, especially if your workshop has specific safety requirements.
- Timelines: They should provide realistic timelines for the project and adhere to agreed-upon schedules.
- Contract and Terms: Review the contract carefully, ensuring all details, including materials, costs, and project milestones, are clearly outlined.
By considering these factors and conducting thorough research, you can identify a professional workshop flooring provider in Perth who will meet your needs and deliver a high-quality result.
Frequently Asked Questions about Workshop Flooring in Perth
What is the best floor surface for the workshop?
- Epoxy Flooring: Epoxy coatings are a popular choice for workshops in Perth. They are highly durable, chemical-resistant, easy to clean, and provide a smooth, seamless surface. Epoxy floors are ideal for heavy machinery, automotive workshops, and areas where spills are common.
- Polished Concrete: Polished concrete is a cost-effective and durable option. It’s resistant to heavy equipment, easy to clean, and can be customized with various finishes. It’s a popular choice for workshops where a more industrial look is preferred.
- Rubber Flooring: Rubber flooring provides excellent impact resistance and is comfortable to stand on, making it suitable for workshops where workers spend long hours on their feet. It’s often used in gyms, mechanic shops, and areas where sound absorption is needed.
- Interlocking Tiles or Mats: Interlocking tiles or mats are versatile and easy to install. They come in various materials like PVC, vinyl, or rubber and can be replaced individually if damaged. They work well for workshops with changing layout needs.
- Painted Concrete: While not as durable as epoxy coatings, painting the concrete floor with industrial-grade paint is a budget-friendly option. It provides a clean and dust-free surface, making it easier to maintain.
- Vinyl Flooring: Vinyl flooring is resistant to chemicals, easy to clean, and provides some cushioning for workers’ comfort. It’s a suitable option for workshops with a mix of office and workspace.
- Linoleum: Linoleum is eco-friendly and offers good resistance to chemicals and stains. It’s a less common choice for workshops but can work well if sustainability is a priority.
The best floor surface for your workshop in Perth depends on your specific needs, budget, and the type of work conducted. Consider factors such as durability, ease of maintenance, resistance to chemicals and spills, and your aesthetic preferences. It’s advisable to consult with a professional flooring provider who can assess your workshop’s requirements and recommend the most suitable flooring solution.
How thick should a workshop floor be?
The thickness of a workshop floor depends on several factors, including the type of flooring material used, the expected load-bearing capacity, and the specific requirements of your workshop.
Here are some general guidelines for workshop floor thickness based on common flooring materials:
- Concrete Slab: If you’re using a standard concrete slab for your workshop floor, a minimum thickness of 4 inches (about 100 mm) is typically recommended. However, for heavier loads or commercial applications, a thicker slab may be necessary. In industrial settings, slab thickness can range from 4 to 6 inches or more.
- Epoxy Flooring: Epoxy coatings are typically applied in multiple layers. The total thickness of an epoxy floor system can vary but often ranges from 20 to 30 mil (0.02 to 0.03 inches) per coat. Multiple coats are applied to achieve the desired thickness and durability.
- Rubber Flooring: The thickness of rubber flooring tiles or rolls can vary. Common thicknesses for rubber flooring in workshops range from 3/8 inch (about 9.5 mm) to 1/2 inch (about 12.7 mm) or more. Thicker rubber provides more cushioning and durability.
- Interlocking Tiles or Mats: Interlocking tiles or mats come in various thicknesses, typically ranging from 1/4 inch (about 6.35 mm) to 3/4 inch (about 19 mm) or more. Thicker tiles offer more cushioning and insulation.
The choice of thickness should consider the specific requirements of your workshop, including the weight of equipment and machinery, the potential for heavy traffic, and the need for insulation or cushioning for worker comfort.
Thicker floors generally offer better durability and load-bearing capacity, but they may also increase construction costs.
It’s essential to consult with a professional flooring contractor or engineer who can assess your workshop’s requirements and recommend the appropriate floor thickness based on your specific needs and budget. They can ensure that your workshop floor is designed to withstand the demands of your operation effectively.
Hear From Our Satisfied Customers
The whole team take great pride in their work and the quality cannot be faulted.