Struggling with Unsafe or Worn Floors? Discover Warehouse Flooring Perth
2-Year Product & Workmanship Warranty
Transform your space with durable and cost-effective warehouse flooring solutions
Cracked, slippery, or uneven warehouse flooring isn’t just an eyesore—it’s a safety hazard and a potential drain on productivity in Perth.
Worn-out flooring can lead to accidents, costly repairs, and unnecessary downtime, impacting your bottom line and the well-being of your team.
At PM Industries, we specialise in providing durable, high-quality flooring solutions designed to meet the demands of Perth businesses.
Whether you need a non-slip surface, heavy-duty epoxy, or a seamless finish to withstand heavy machinery, our tailored solutions are engineered to enhance safety, durability, and efficiency in your workspace.
- All services come with a 100% Satisfaction Guarantee
- 25+ years of industry experience delivering premium results
- Top-quality products sourced from reputable Australian manufacturers
Free Quotes Within 48 Hours
With years of experience in the industry, our skilled team has earned a reputation for excellence and reliability. We combine advanced materials with precision craftsmanship to deliver flooring that not only meets but exceeds industry standards.
When you partner with PM Industries, you’re choosing a trusted local expert who understands the unique challenges of Perth’s business environments.
Contact us today at 0436 837 699 or claim your 100% obligation-free quote online.
On this Page:
- When is the right time to upgrade warehouse flooring?
- How long does warehouse flooring take to install?
- How can I identify a professional warehouse flooring installer?
- What are the best flooring materials for Perth’s climate?
- How do I maintain and clean my floors to extend their lifespan?
- What safety features should I consider when choosing warehouse flooring?
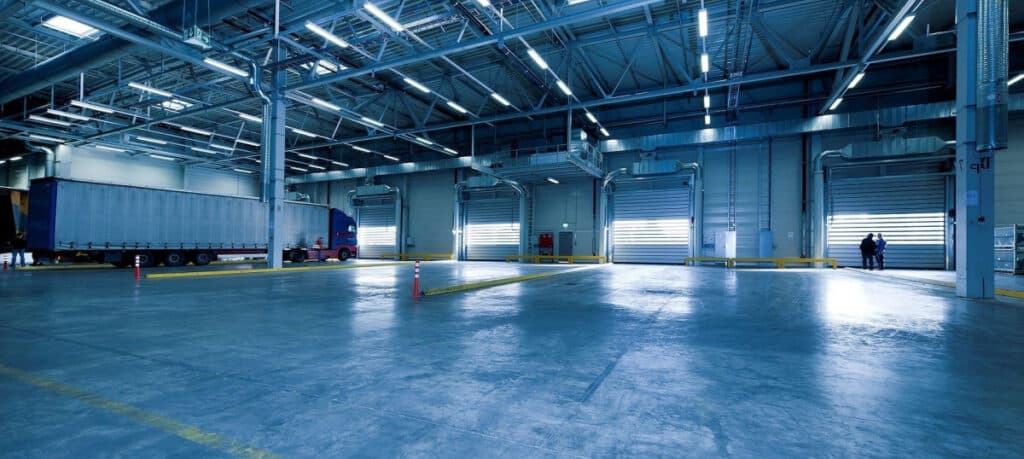
When is the right time to upgrade warehouse flooring?
Deciding whether your warehouse needs new flooring can depend on several factors:
- Visible Wear and Tear: Cracks, chips, and uneven surfaces are clear indicators that your current flooring may be compromised. These issues can worsen over time, leading to increased repair costs and safety hazards.
- Frequent Accidents or Slips: If your team is experiencing regular slips or falls, it might be time to invest in non-slip, safety-enhancing flooring solutions.
- High Foot or Equipment Traffic: Warehouses with heavy machinery or constant foot traffic require robust flooring that can withstand wear and tear. If your flooring is showing signs of strain, consider upgrading.
- Hygiene or Maintenance Issues: Stained, porous, or hard-to-clean surfaces could mean your flooring isn’t up to the task. Modern solutions like epoxy flooring are easier to clean and maintain, improving hygiene standards.
- Business Expansion or Renovation: If you’re upgrading your warehouse layout, adding new equipment, or expanding operations, a flooring update can ensure your space is ready to handle increased demands.
If any of these signs sound familiar, it may be time to explore professional flooring options. PM Industries can assess your space and recommend tailored solutions to meet your needs.
How long does warehouse flooring take to install?
Installation timelines depend on several factors, including the size of the area, the type of flooring, and the condition of the existing surface. Here’s a general breakdown:
Surface Preparation: Preparing the floor, such as cleaning, repairing, diamond grinding and levelling, typically takes 1–2 days, depending on the condition of the existing surface.
Application of Flooring Material:
- Epoxy Coating: Applying epoxy can take 1–3 days, as multiple coats are often required with curing time in between.
- Polyurethane Flooring: Installation usually takes 1–2 days, with fast curing times.
- Concrete Polishing or Sealing: This process generally takes 2–4 days, depending on the size and complexity.
Curing and Setting Time: Most industrial flooring systems need a curing period to ensure durability. This can range from 24 hours for light use to 5–7 days for heavy equipment and full load-bearing capacity.
In total, a typical warehouse flooring project can take anywhere from 3–10 days. PM Industries works efficiently to minimise downtime while ensuring the highest quality.
How can I identify a professional warehouse flooring installer?
Choosing a professional flooring provider is crucial for achieving durable, safe, and cost-effective results. Here are some key factors to consider:
- Experience and Expertise: Look for providers with a proven track record. Check their portfolio for similar projects and assess their ability to handle your specific needs.
- Material Quality: Ensure the provider uses high-quality materials that suit your warehouse’s requirements, such as epoxy for durability or polyurethane for flexibility.
- Certifications and Compliance: A professional provider will meet industry standards and local regulations, ensuring your flooring is safe and reliable.
- Customer Reviews and References: Seek feedback from previous clients to gauge customer satisfaction, workmanship, and post-installation support.
- Customisation and Consultation: A reputable provider offers tailored solutions and thorough consultations, understanding that every warehouse has unique demands.
- Warranty and Support: Check if the company provides warranties and after-sales support, demonstrating confidence in their work.
Contact us today at 0436 837 699 or claim your 100% obligation-free quote online.
Frequently Asked Questions About Warehouse Flooring in Perth
What are the best flooring materials for Perth’s climate?
Perth’s climate, characterised by warm summers and occasional wet conditions, demands flooring materials that are durable, heat-resistant, and moisture-resistant. We recommend:
- Epoxy Flooring: Epoxy coatings are highly durable, resistant to heat and moisture, and provide a seamless, easy-to-clean surface. This makes them an excellent choice for Perth warehouses experiencing high temperatures and occasional humidity.
- Polished Concrete: Polished concrete is another popular option due to its ability to withstand heavy loads, resist moisture, and reflect light, enhancing visibility in warehouse spaces.
- Polyurethane Flooring: Polyurethane is known for its flexibility, which helps it resist cracking under temperature fluctuations. It’s ideal for warehouses where heat exposure is significant.
- Vinyl Flooring: For areas of the warehouse with light traffic, vinyl flooring offers a cost-effective solution that resists heat and moisture while being easy to install and maintain.
- Anti-Slip Coatings: Incorporating anti-slip finishes into any of these materials is essential for ensuring safety in wet or high-traffic conditions.
How do I maintain and clean my floors to extend their lifespan?
Proper flooring maintenance and cleaning extend its lifespan and enhance safety and functionality. Here’s how to care for your flooring effectively:
Regular Cleaning Routine:
- Sweep or vacuum daily to remove debris that can cause wear and tear.
- Use a damp mop or an industrial floor scrubber with a pH-neutral cleaner to prevent stains and maintain the finish.
Prompt Spill Management:
- Address spills immediately, especially if you’re using epoxy or polished concrete, to prevent staining or slipping hazards. Use absorbent materials and clean with appropriate solutions.
Protect High-Traffic Areas:
- Use protective mats or coverings in areas with heavy machinery or foot traffic to reduce surface stress.
Inspect for Damage:
- Regularly inspect your flooring for cracks, chips, or signs of wear. Early detection allows for quick repairs, preventing further damage.
Apply Protective Coatings:
- Periodically reapply protective coatings, such as sealers for concrete or a fresh epoxy layer, to maintain durability and appearance.
Avoid Harsh Chemicals:
- Use cleaning products recommended for your flooring type. Harsh chemicals can degrade finishes and compromise the floor’s integrity.
What safety features should I consider when choosing warehouse flooring?
Safety is paramount in a warehouse setting, and selecting the right flooring can significantly reduce risks. Here are key safety features to prioritise:
Slip Resistance: Opt for flooring with anti-slip properties to prevent accidents, especially in areas prone to spills or moisture. Textured epoxy coatings and anti-slip additives are excellent choices.
Durability and Load Resistance: Ensure the flooring can withstand heavy machinery, forklifts, and high foot traffic without cracking or wearing down, which could create safety hazards.
Chemical Resistance: For warehouses handling chemicals, select flooring resistant to spills and corrosion to maintain safety and longevity.
Seamless Surface: Seamless floors eliminate gaps and cracks that could trip workers or catch machinery wheels.
High Visibility Markings: Flooring that allows for clear demarcation of safety zones, walkways, and equipment areas improves organisation and reduces the risk of collisions or missteps.
Shock Absorption and Flexibility: Flexible materials like polyurethane help absorb impacts, reducing the risk of breakage or injury from dropped items.
Hear From Our Satisfied Customers
The whole team take great pride in their work and the quality cannot be faulted.